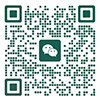
在印制(zhì)電(diàn)路加工中﹐氨性蝕刻是一個(gè)較為(wèi)精細和(hé)覆雜的化學反應過程,卻又是一項易于進行(xíng)的工作(zuò)。隻要工藝上(shàng)達至調通(tōng)﹐就可(kě)以進行(xíng)連續性的生(shēng)産, 但(dàn)關鍵是開(kāi)機以後就必需保持連續的工作(zuò)狀态﹐不适宜斷斷續續地生(shēng)産。蝕刻工藝對設備狀态的依賴性極大(dà),故必需時(shí)刻使設備保持在良好的狀态。
目前﹐無論使用何種蝕刻液﹐都必須使用高(gāo)壓噴淋﹐而為(wèi)了獲得(de)較整齊的側邊線條和(hé)高(gāo)質量的蝕刻效果﹐對噴嘴的結構和(hé)噴淋方式的選擇都必須更為(wèi)嚴格。
對于優良側面效果的制(zhì)造方式﹐外界均有(yǒu)不同的理(lǐ)論、設計(jì)方式和(hé)設備結構的研究,而這些(xiē)理(lǐ)論卻往往是人(rén)相徑庭的。但(dàn)是有(yǒu)一條最基本的原則已被公認并經化學機理(lǐ)分析證實﹐就是盡速讓金屬表面不斷地接觸新鮮的蝕刻液。
在氨性蝕刻中﹐假定所有(yǒu)參數(shù)不變﹐那(nà)麽蝕刻的速率将主要由蝕刻液中的氨(NH3)來(lái)決定。因此, 使用新鮮溶液與蝕刻表面相互作(zuò)用﹐其主要目的有(yǒu)兩個(gè)﹕沖掉剛産生(shēng)的銅離子及不斷為(wèi)進行(xíng)反應供應所需要的氨(NH3)。
在印制(zhì)電(diàn)路工業的傳統知識裏﹐特别是印制(zhì)電(diàn)路原料的供貨商們皆認同﹐并得(de)經驗證實﹐氨性蝕刻液中的一價銅離子含量越低(dī)﹐反應速度就越快。
事實上(shàng)﹐許多(duō)的氨性蝕刻液産品都含有(yǒu)價銅離子的特殊配位基(一些(xiē)複雜的溶劑)﹐其作(zuò)用是降低(dī)一價銅離子(産品具有(yǒu)高(gāo)反應能力的技(jì)術(shù)秘訣)﹐可(kě)見一價銅離子的影(yǐng)響是不小(xiǎo)的。
将一價銅由5000ppm降至50ppm,蝕刻速率即提高(gāo)一倍以上(shàng)。
由于在蝕刻反應的過程中會(huì)生(shēng)成大(dà)量的一價銅離子,而一價銅離子又總是與氨的絡合基緊緊的結合在一起﹐所以要保持其含量近于零是十分困難的。
而采用噴淋的方式卻可(kě)以達到通(tōng)過大(dà)氣中氧的作(zuò)用将一價銅轉換成二價銅,并去除一價銅,這就是需要将空(kōng)氣通(tōng)入蝕刻箱的一個(gè)功能性的原因。但(dàn)是如果空(kōng)氣太多(duō)﹐又會(huì)加速溶液中的氨的損失而使PH值下降﹐使蝕刻速率降低(dī)。氨在溶液中的變化量也是需要加以控制(zhì)的,有(yǒu)一些(xiē)用戶采用将純氨通(tōng)入蝕刻儲液槽的做(zuò)法,但(dàn)這樣做(zuò)必須加一套PH計(jì)控制(zhì)系統,當自動監測的PH結果低(dī)于默認值時(shí)﹐便會(huì)自動進行(xíng)溶液添加。
在相關的化學蝕刻(亦稱之為(wèi)光化學蝕刻或PCH)領域中﹐研究工作(zuò)已經開(kāi)始﹐并達至蝕刻機結構設計(jì)的階段。此方法所使用的溶液為(wèi)二價銅,不是氨-銅蝕刻, 它将有(yǒu)可(kě)能被用在印制(zhì)電(diàn)路工業中。在PCH工業中,蝕刻銅箔的典型厚度為(wèi)5到10密耳(mils),有(yǒu)些(xiē)情況下厚度卻相當大(dà)。它對蝕刻參數(shù)的要求經常比PCB工業更為(wèi)苛刻。有(yǒu)一項來(lái)自PCM工業系統但(dàn)尚未正式發表的研究成果﹐相信其結果将會(huì)令人(rén)耳目一新。
由于有(yǒu)雄厚的項目基金支持﹐因此研究人(rén)員有(yǒu)能力從長遠意議上(shàng)對蝕刻裝置的設計(jì)思想進行(xíng)改變﹐同時(shí)研究這些(xiē)改變所産生(shēng)的效果。
比如說﹐與錐形噴嘴相比﹐采用扇形噴嘴的設計(jì)效果更佳﹐而且噴淋集流腔(即噴嘴擰進去的那(nà)一段管)也有(yǒu)一個(gè)安裝角度﹐對進入蝕刻艙中的工件呈30度噴射﹐若不進行(xíng)這樣的改變, 集流腔上(shàng)噴嘴的安裝方式将會(huì)導緻每個(gè)相領噴嘴的噴射角度都不一緻。第二組噴嘴各自的噴淋面與第一組相對應的皆略有(yǒu)不同(它表示了噴淋的工作(zuò)情況),使噴射出的溶液形狀成為(wèi)叠加或交叉的狀态。
理(lǐ)論上(shàng)﹐如果溶液形狀相互交叉,該部分的噴射力就會(huì)降低(dī)而不能有(yǒu)效地将蝕刻表面上(shàng)的舊(jiù)溶液沖掉使新溶液與其接觸。 在噴淋面的邊緣處,這種情況尤為(wèi)突出,其噴射力比垂直噴射要小(xiǎo)得(de)多(duō)。這項研究發現﹐最新的設計(jì)參數(shù)是65磅/平方英寸(即4+Bar)。
每個(gè)蝕刻過程和(hé)每種實用的溶液都有(yǒu)一個(gè)最佳的噴射壓力的問題﹐就目前而言﹐蝕刻艙內(nèi)噴射壓力在30磅/平方英(2Bar)以上(shàng)的情況微乎其微。
但(dàn)有(yǒu)一個(gè)原則﹐一種蝕刻溶液的密度(即比重或玻美度)越高(gāo)﹐最佳的噴射壓力也應越高(gāo)。當然,這并非單一的參數(shù),另一個(gè)重要的參數(shù)是在溶液中控制(zhì)其反應率的相對淌度(或遷移率)。
1)關于蝕刻狀态不相同的問題
大(dà)量涉及蝕刻面的質量問題都集中在上(shàng)闆面被蝕刻的部分,而這些(xiē)問題來(lái)自于蝕刻劑所産生(shēng)的膠狀闆結物的影(yǐng)響。對這一點的了解是十分重要的, 因膠狀闆結物堆積在銅表面上(shàng)。一方面會(huì)影(yǐng)響噴射力,另一方面會(huì)阻檔了新鮮蝕刻液的補充,使蝕刻的速度被降低(dī)。正因膠狀闆結物的形成和(hé)堆積, 使得(de)基闆上(shàng)下面的圖形的蝕刻程度不同,先進入的基闆因堆積尚未形成,蝕刻速度較快, 故容易被徹底地蝕刻或造成過腐蝕,而後進入的基闆因堆積已形成,而減慢了蝕刻的速度。
2)蝕刻設備的維護
維護蝕刻設備的最關鍵因素就是要保證噴嘴的高(gāo)清潔度及無阻塞物,使噴嘴能暢順地噴射。阻塞物或結渣會(huì)使噴射時(shí)産生(shēng)壓力作(zuò)用, 沖擊闆面。而噴嘴不清潔,則會(huì)造成蝕刻不均勻而使整塊電(diàn)路闆報廢。
明(míng)顯地,設備的維護就是更換破損件和(hé)磨損件,因噴嘴同樣存在着磨損的問題, 所以更換時(shí)應包括噴嘴。此外,更為(wèi)關鍵的問題是要保持蝕刻機沒有(yǒu)結渣﹐因很(hěn)多(duō)時(shí)結渣堆積過多(duō)會(huì)對蝕刻液的化學平衡産生(shēng)影(yǐng)響。同樣地,如果蝕刻液出現化學不平衡,結渣的情況就會(huì)愈加嚴重。蝕刻液突然出現大(dà)量結渣時(shí),通(tōng)常是一個(gè)信号,表示溶液的平衡出現了問題, 這時(shí)應使用較強的鹽酸作(zuò)适當的清潔或對溶液進行(xíng)補加。
另外,殘膜也會(huì)産生(shēng)結渣物。極少(shǎo)量的殘膜溶于蝕刻液中﹐形成銅鹽沈澱。這表示前道(dào)去膜工序做(zuò)得(de)不徹底,去膜不良往往是邊緣膜與過電(diàn)鍍共同造成的結果。
3)蝕刻過程中應注意的問題
減少(shǎo)側蝕和(hé)突沿﹐提高(gāo)蝕刻系數(shù)
側蝕會(huì)産生(shēng)突沿。通(tōng)常印制(zhì)闆在蝕刻液中的時(shí)間(jiān)越長,側蝕的情況越嚴重。側蝕将嚴重影(yǐng)響印制(zhì)導線的精度,嚴重的側蝕将不可(kě)能制(zhì)作(zuò)精細導線。當側蝕和(hé)突沿降低(dī)時(shí),蝕刻系數(shù)就會(huì)升高(gāo),高(gāo)蝕刻系數(shù)表示有(yǒu)保持細導線的能力,使蝕刻後的導線能接近原圖尺寸。無論是錫-鉛合金,錫﹐錫-鎳合金或鎳的電(diàn)鍍蝕刻劑, 突沿過度時(shí)都會(huì)造成導線短(duǎn)路。因為(wèi)突沿容易撕裂下來(lái),在導線的兩點之間(jiān)形成電(diàn)的拆接。
4)影(yǐng)響側蝕的因素有(yǒu)很(hěn)多(duō)﹐下面将概述幾點﹕
1·蝕刻方式﹕
浸泡和(hé)鼓泡式蝕刻會(huì)造成較大(dà)的側蝕﹐潑濺和(hé)噴淋式蝕刻的側蝕較小(xiǎo)﹐尤以噴淋蝕刻的效果最好。
2·蝕刻液的種類﹕
不同的蝕刻液,其化學組分不相同﹐蝕刻速率就不一樣﹐蝕刻系數(shù)也不一樣。
例如﹕酸性氯化銅蝕刻液的蝕刻系數(shù)通(tōng)常為(wèi)3﹐而堿性氯化銅蝕刻系數(shù)可(kě)達到4。
3·蝕刻速率:
蝕刻速率慢會(huì)造成嚴重側蝕。提高(gāo)蝕刻質量與加快蝕刻速率有(yǒu)很(hěn)大(dà)的關系,蝕刻速度越快,基闆在蝕刻中停留的時(shí)間(jiān)越短(duǎn)﹐側蝕量将越小(xiǎo)﹐蝕刻出的圖形會(huì)更清晰整齊。
4·蝕刻液的PH值:
堿性蝕刻液的PH值較高(gāo)時(shí)﹐側蝕會(huì)增大(dà)。為(wèi)了減少(shǎo)側蝕﹐PH值一般應控制(zhì)在8.5以下。
蝕刻液的密度:
堿性蝕刻液的密度太低(dī)會(huì)加重側蝕﹐選用高(gāo)銅濃度的蝕刻液對減少(shǎo)側蝕非常有(yǒu)利。
5)銅箔厚度:
要達到最小(xiǎo)側蝕的細導線的蝕刻﹐最好采用(超)薄銅箔。而且線寬越細﹐銅箔厚度應越薄。因為(wèi),銅箔越薄在蝕刻液中的時(shí)間(jiān)會(huì)越短(duǎn)﹐側蝕量就越小(xiǎo)。
提高(gāo)基闆與基闆之間(jiān)蝕刻速率的一緻性
在連續的闆蝕刻中,蝕刻速率的一緻性越高(gāo),越能獲得(de)蝕刻均勻的闆。要達到這一個(gè)要求,必須保證蝕刻液在蝕刻的整個(gè)過程始終保持在最佳的蝕刻狀态。這就要選擇容易再生(shēng)和(hé)補償, 而蝕刻速率又容易控制(zhì)的蝕刻液,并選用能提供恒定的操作(zuò)條件和(hé)能自動控制(zhì)各種溶液參數(shù)的工藝和(hé)設備, 通(tōng)過控制(zhì)溶銅量、PH值、溶液的濃度、溫度及溶液流量的均勻性(噴淋系統或噴嘴,以至噴嘴的擺動)等來(lái)實現蝕刻速率的一緻性。
提高(gāo)基闆表面的蝕刻速率的均勻性
基闆的上(shàng)下兩面以及闆面上(shàng)各部位的蝕刻的均勻性,皆決定于闆表面受到蝕刻劑流量的均勻性所影(yǐng)響。
在蝕刻的過程中﹐上(shàng)下闆面的蝕刻速率往往并不一緻。一般來(lái)說﹐下闆面的蝕刻速率會(huì)高(gāo)于上(shàng)闆面。因為(wèi)上(shàng)闆面有(yǒu)溶液的堆積﹐減弱了蝕刻反應的進行(xíng), 但(dàn)可(kě)以通(tōng)過調整上(shàng)下噴嘴的噴淋壓力來(lái)解決上(shàng)下闆面蝕刻不均的現象。
蝕刻工藝的一個(gè)普遍問題是在相同的時(shí)間(jiān)裏使全部闆面都蝕刻幹淨是很(hěn)難做(zuò)到的。因基闆的邊緣位置比中心部位蝕刻得(de)更快, 故很(hěn)難做(zuò)到同時(shí)使全部蝕刻都幹淨。而采用噴淋系統并使噴嘴擺動噴射是一個(gè)有(yǒu)效的解決措施。要更進一步地改善,可(kě)以透過對闆中心和(hé)邊緣處不同的噴淋壓力,以及對闆前沿和(hé)闆後端采用間(jiān)歇蝕刻的方法﹐達到整個(gè)闆面的蝕刻均勻性。
提高(gāo)安全處理(lǐ)和(hé)蝕刻薄銅箔及薄層壓闆的能力
在蝕刻薄層闆時(shí)(如:多(duō)層闆的內(nèi)層闆),基闆容易卷繞在滾輪和(hé)傳送輪上(shàng)而造成廢品,所以蝕刻內(nèi)層闆的設備必須要保證能平穩地及可(kě)靠地處理(lǐ)薄的層壓闆。現時(shí), 許多(duō)設備制(zhì)造商在蝕刻機內(nèi)附加齒輪或滾輪來(lái)防止卷繞的情況,但(dàn)更好的方法卻是附加左右搖擺的四氟乙烯塗包線作(zuò)為(wèi)薄層壓闆傳送時(shí)的支撐物。
對于薄銅箔(例如1/2或1/4盎司)的蝕刻,必須保證銅面不被擦傷或劃傷。有(yǒu)時(shí)較劇(jù)烈的振顫都有(yǒu)可(kě)能損傷銅箔。
6)減少(shǎo)污染的問題
銅對水(shuǐ)的污染是印制(zhì)電(diàn)路生(shēng)産中普遍存在的問題﹐而氨堿蝕刻液的使用更加重了這個(gè)問題。因為(wèi)銅與氨絡合﹐不容易用離子交換法或堿沈澱法除去。所以﹐采用無銅的添加液來(lái)漂洗闆子(第二次噴淋操作(zuò)的方法)﹐可(kě)大(dà)大(dà)地減少(shǎo)銅的排出量。然後﹐再用空(kōng)氣刀在水(shuǐ)漂洗之前将闆面上(shàng)多(duō)餘的溶液去除﹐從而減輕了水(shuǐ)對銅的蝕刻的鹽類的漂洗負擔。
在自動蝕刻系統中, 銅濃度是以比重來(lái)控制(zhì)的。在印制(zhì)闆的蝕刻過程中﹐随着銅不斷地被溶解﹐當溶解的比重不斷升高(gāo)至超過一定的數(shù)值時(shí)﹐系統便會(huì)自動補加氯化铵和(hé)氨的水(shuǐ)溶液﹐使比重調整回合适的範圍。一般的比重應控制(zhì)在18~240Be。
溶液PH值的影(yǐng)響
蝕刻液的PH值應保持在8.0~8.8之間(jiān)。若PH值下降到8.0以下時(shí),将會(huì)對金屬抗蝕層不利。
另一方面﹐蝕刻液中的銅不能被完全絡合成銅氨絡離子﹐使溶液在槽底形成泥狀沈澱, 而這些(xiē)沈澱物能在加熱器(qì)上(shàng)結成硬皮﹐可(kě)能會(huì)損壞加熱器(qì)﹐還(hái)會(huì)使泵和(hé)噴嘴受到堵塞﹐給蝕刻造成困難。如果溶液PH值過高(gāo)﹐蝕刻液中的氨過飽和(hé)﹐遊離氨便會(huì)釋放到大(dà)氣之中﹐導緻環境污染。再說﹐溶液的PH值增大(dà)也會(huì)增大(dà)側蝕的程度﹐繼而影(yǐng)響蝕刻的精度。
7)氯化铵含量的影(yǐng)響
通(tōng)過蝕刻再生(shēng)的化學反應可(kě)以看出﹕﹝Cu(NH3)2﹞1+的再生(shēng)需要有(yǒu)過量的NH3和(hé)NH4CL存在。如果溶液中缺乏NH4CL,而使大(dà)量的﹝Cu(NH3)2﹞1+得(de)不到再生(shēng)﹐蝕刻速率就會(huì)降低(dī)﹐以至失去蝕刻能力。所以﹐氯化铵的含量對蝕刻速率影(yǐng)響很(hěn)大(dà)。随着蝕刻的進行(xíng)﹐要不斷補加氯化铵。但(dàn)是﹐溶液中CL含量過高(gāo)會(huì)引起抗蝕層被浸蝕。一般蝕刻液中NH4CL含量應在150g/L左右。
8)溫度的影(yǐng)響
蝕刻速率與溫度有(yǒu)着很(hěn)大(dà)的關系, 蝕刻速率會(huì)随着溫度升高(gāo)而加快﹐蝕刻液溫度低(dī)于40℃﹐蝕刻速率會(huì)很(hěn)慢﹐而蝕刻速率過慢則會(huì)增大(dà)側蝕量﹐影(yǐng)響蝕刻質量。
當溫度高(gāo)于60℃﹐蝕刻速率會(huì)明(míng)顯地增大(dà),但(dàn)NH3的揮發量也大(dà)大(dà)地增加﹐導緻環境污染并使蝕刻液中化學組份比例失調。故一般應控制(zhì)在45℃~55℃為(wèi)宜。
9)蝕刻液的調整
10)自動控制(zhì)調整
随着蝕刻的進行(xíng), 蝕刻液中銅的含量不斷增加﹐比重亦逐漸升高(gāo)。當蝕刻液中銅濃度達到一定的高(gāo)度時(shí)就要及時(shí)調整。在自動控制(zhì)補加裝置中﹐是利用比重控制(zhì)器(qì)來(lái)控制(zhì)蝕刻液的比重。當比重升高(gāo)時(shí)﹐會(huì)自動排放出溶液﹐并添加新的補加液﹐使蝕刻液的比重調整到允許的範圍。補加液要事先配制(zhì)好并放入補加桶內(nèi)﹐使補加桶的液面保持在一定的高(gāo)度。
蝕刻過程中常見的問題
1·蝕刻速率降低(dī)
蝕刻速率降低(dī)與許多(duō)因素有(yǒu)關,故需要檢查蝕刻條件(例如﹕溫度、噴淋壓力、溶液比重、PH值和(hé)氯化铵的含量等)﹐使其達到适宜的範圍。
2·蝕刻溶液中出現沈澱
是由于氨的含量過低(dī)(PH值降低(dī))﹐或水(shuǐ)稀釋溶液等原因造成的(例如:冷卻系統漏水(shuǐ)等)。溶液比重過高(gāo)也會(huì)造成沈澱。
3·抗蝕鍍層被浸蝕
是由于蝕刻液PH值過低(dī)或CL含量過高(gāo)所造成的。
4·銅的表面發黑(hēi),蝕刻不動。
蝕刻液中NH4CL的含量過低(dī)所造成的。